At SolarPlace.io, we are dedicated to revolutionizing the solar industry by connecting solution providers with buyers through our AI-driven marketplace and directory service. Our platform offers a seamless way for businesses to showcase their products and services, and for buyers to find exactly what they need.
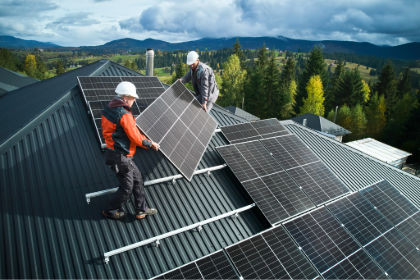
For Solar Businesses
Expand Your Reach: Register your business in our comprehensive directory and gain visibility among a wide audience of potential clients and partners.
Showcase Your Innovations: Highlight your cutting-edge solar technologies and solutions, and stand out in a competitive market.
AI-Driven Marketing Solutions: Leverage our advanced AI tools to optimize your marketing efforts, generate leads, and drive sales.
For Buyers
Find the Perfect Solution: Easily search and discover a wide range of solar products and services tailored to your specific needs.
Trusted Providers: Connect with reputable businesses and industry leaders who are committed to delivering high-quality solar solutions.
Stay Informed: Access the latest news, trends, and innovations in the solar industry through our integrated news platform.
